Will Keating (b. 1996, Newcastle-upon-Tyne) is an artist, craftsperson and potter. He aims to convey a sense of calm, natural beauty, creating objects conducive to slow living. A strong believer in the idea that good pots are “born, not made,” much of Wills practice focuses on creating the conditions in which the best work can occur spontaneously. He uses handmade tools to form locally dug clays, glazing the pots with local rocks and plant ashes before firing them in wood-fired kilns made from hand-formed clay bricks.
Often referring to his background in physics, Wills practice is his way of understanding the world on a fundamental level, exploring how we connect to nature, and to our ancestors, through intrinsic forms, materials and processes. He prioritises the use of found and recycled materials to maintain a sustainable practice with minimal ecological impact, always striving for increased self-sufficiency. Through his work he hopes to inform future practices, as historic, low-impact methods become increasingly lost through the commercialisation of traditional craft practices.
After training under Korean potter Jun Rhee, Will studied Ceramics at Clay College, Stoke-on-Trent from 2022-2024, thanks to a scholarship from the Queen Elizabeth Scholars Trust. Following his graduation, he undertook a period of work and research under the tutelage of potter Matt Hallyburton in Burke County, North Carolina, studying local geology and traditional Catawba Valley throwing and firing techniques.
Will is currently in the process of establishing a new pottery on the edge of Bidston Hill Nature Reserve, on the Wirral Peninsula, Merseyside.
Graduation Exhibition
Clay College, Stoke-on-Trent, Aug 2024
Two years of study culminated in an exhibition of thrown and hand-built pottery, focused on a number of local clays, rocks and plant ashes sourced during that time. Work was fired in a number of different ways to explore the potential of a limited palette of materials local to the artist in Stoke-on-Trent.
Works were left unglazed and fired in a traditional wood-fired anagama kiln, others fired in electric kilns. The bulk of the work was fired in a raw-brick, catenary arch gas kiln built by the artist specifically for the exhibition, detailed in the following section.


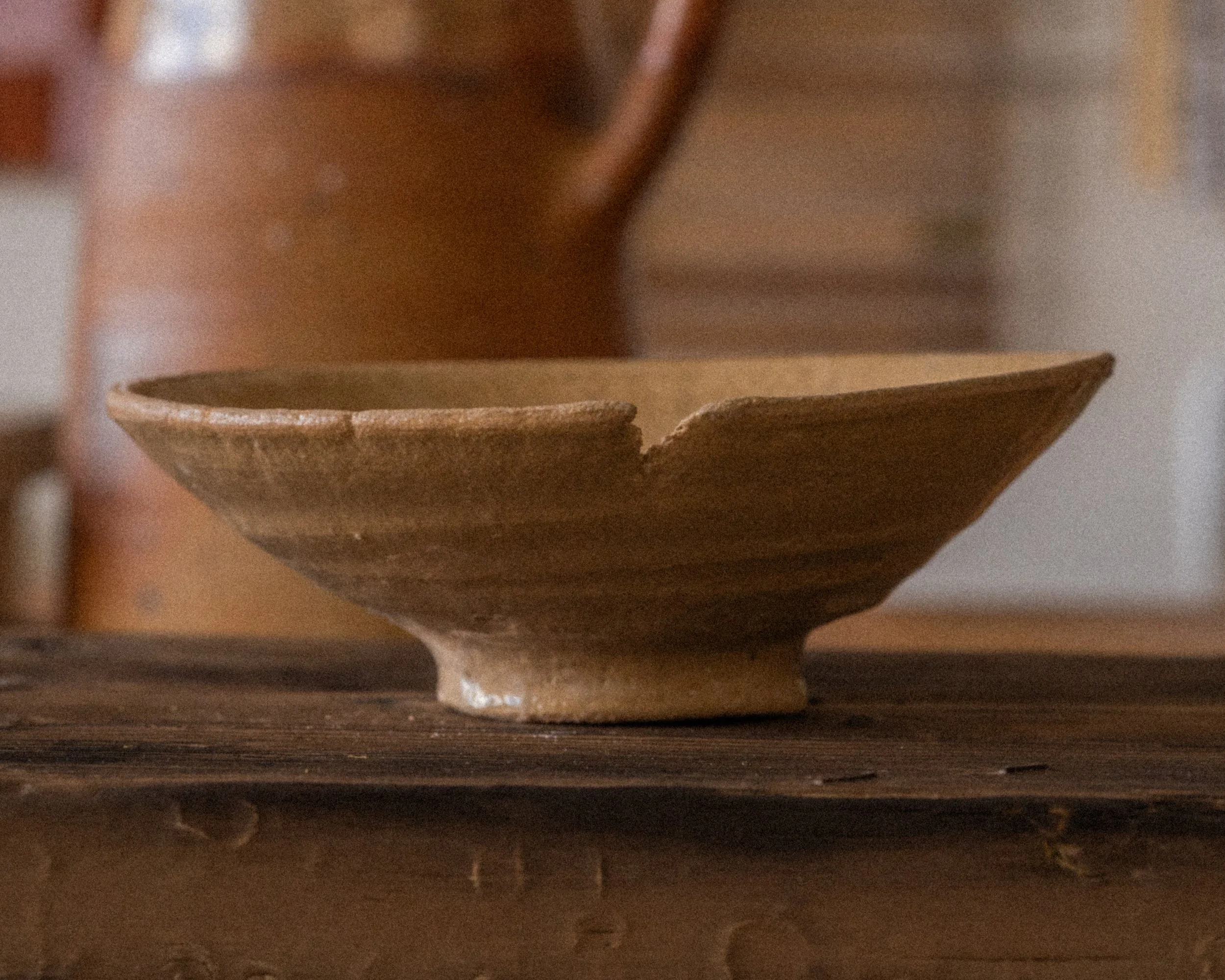
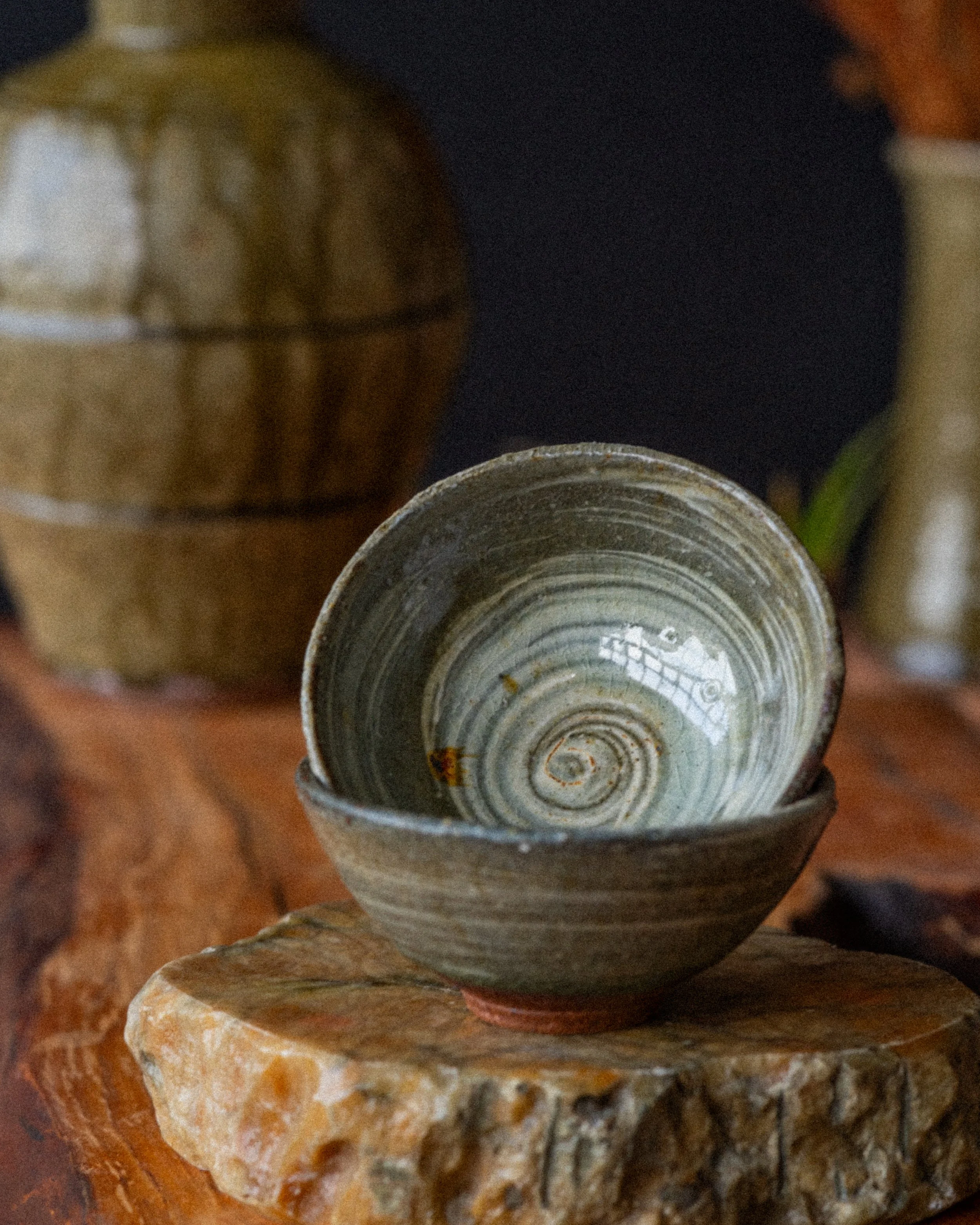
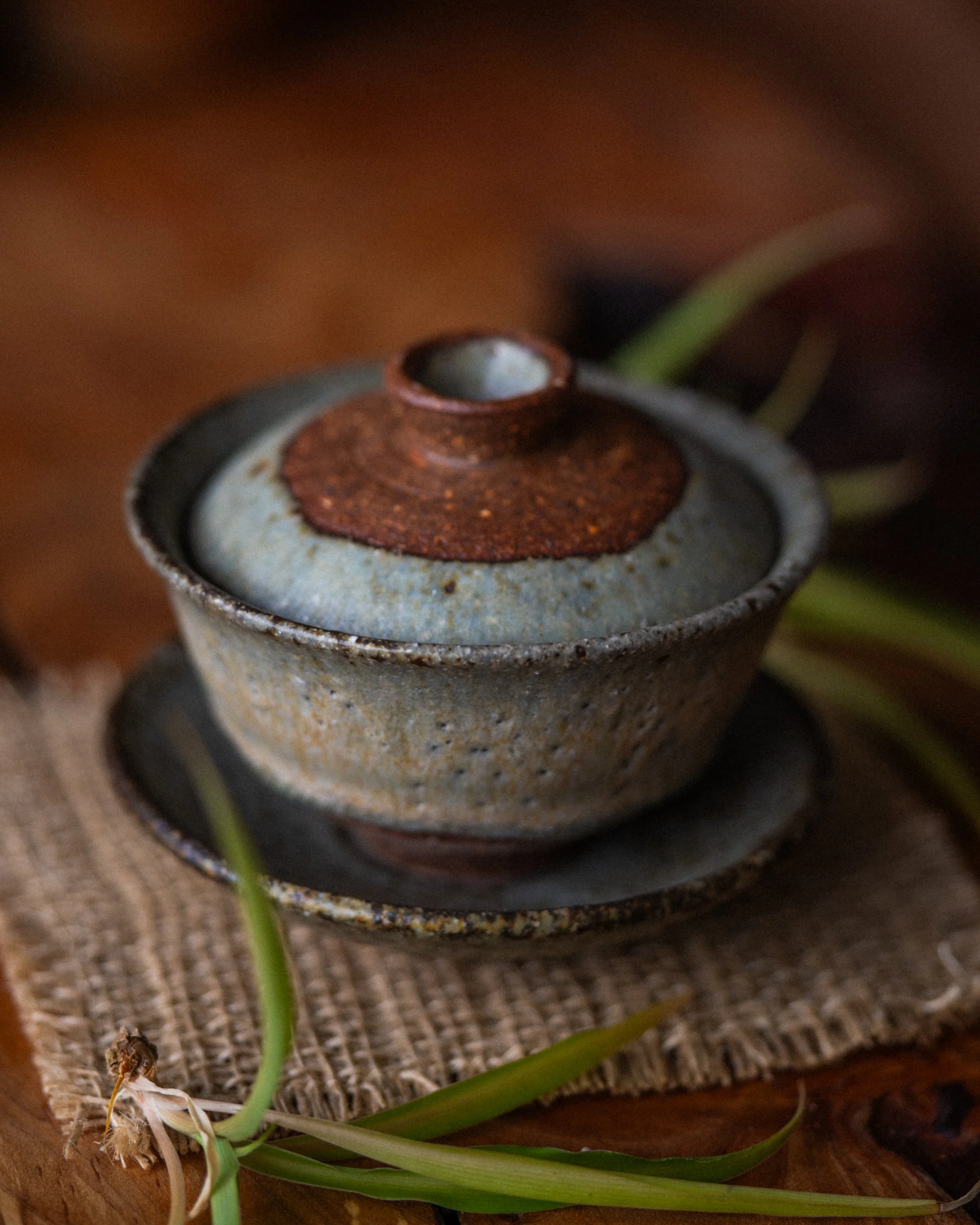
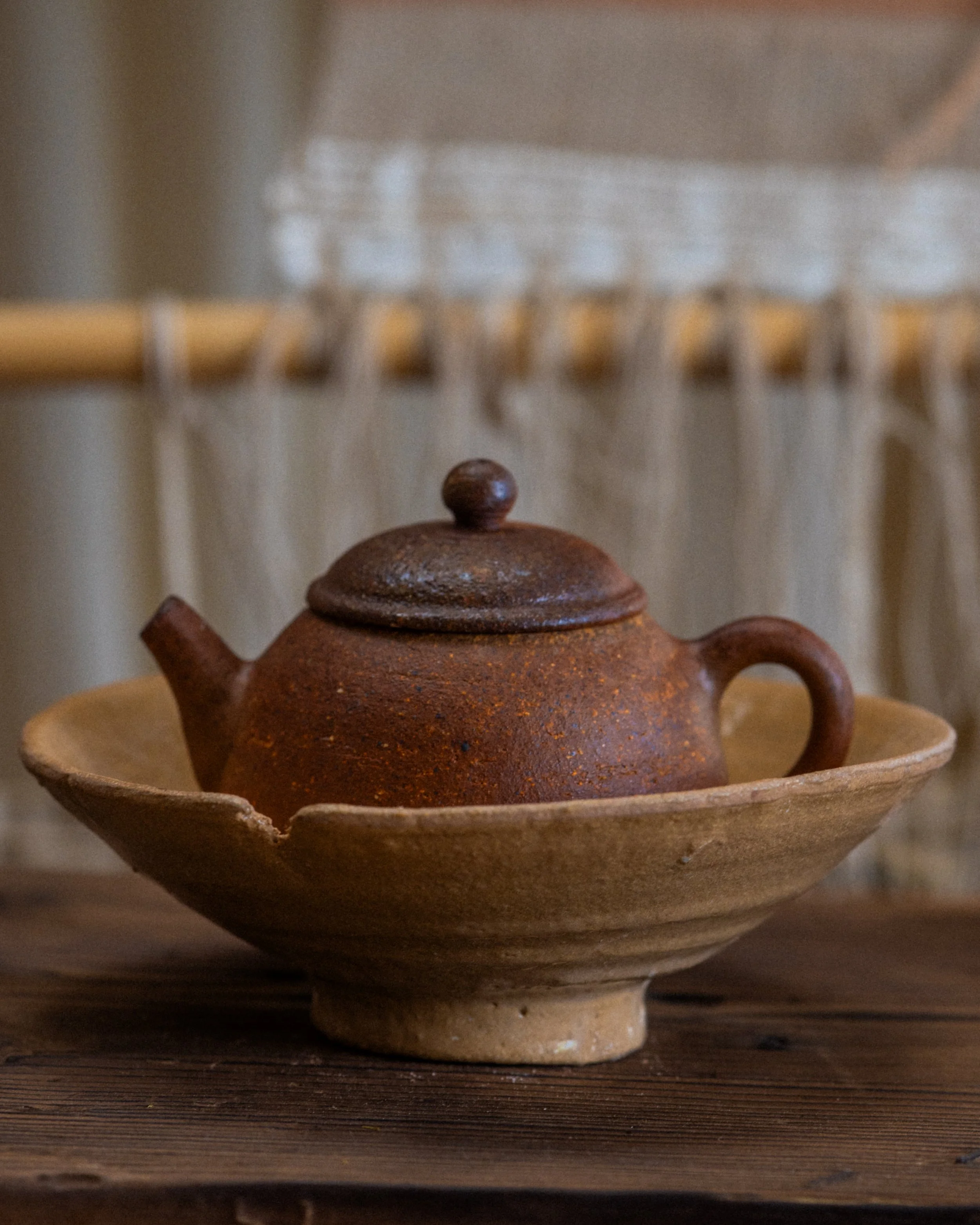
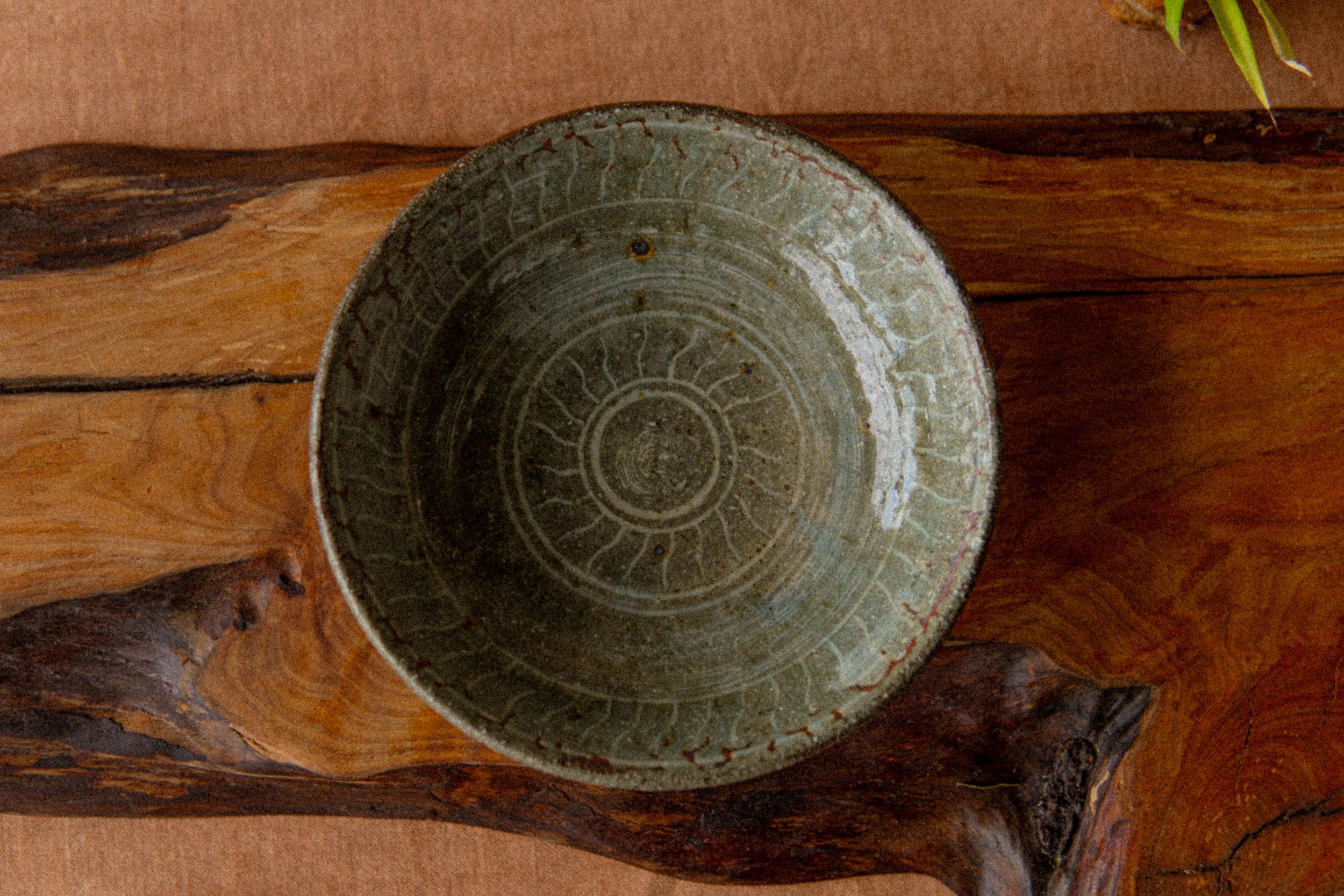
Catenary Arch Kiln
Clay College, 2024
Inspired by the historic practice of creating your own refractories for kiln-building, Will set out to build a propane fired kiln using as little virgin-material as possible. The majority of the insulating bricks used to build the kiln were hand-formed using over 70% recycled waste products from local industry.
The bricks were laid in the unfired state, and the kiln gradually taken up to 1300 degrees over the course of three firings, hardening the bricks in place. The kiln successfully fired to Cone 11 in around 13 hours, proving the efficacy of the handmade, low-cost bricks.